The face milling cutter holder is a specialized tool designed for clamping face milling cutters with four holes. Its main feature is the increased collar contact surface, which provides greater stability during high-speed machining. The holder is typically supplied with lock screws to ensure the cutter is securely fastened, preventing loosening or shifting during use. Common shank sizes include BT40 and BT50, suitable for different CNC machines and machining requirements.
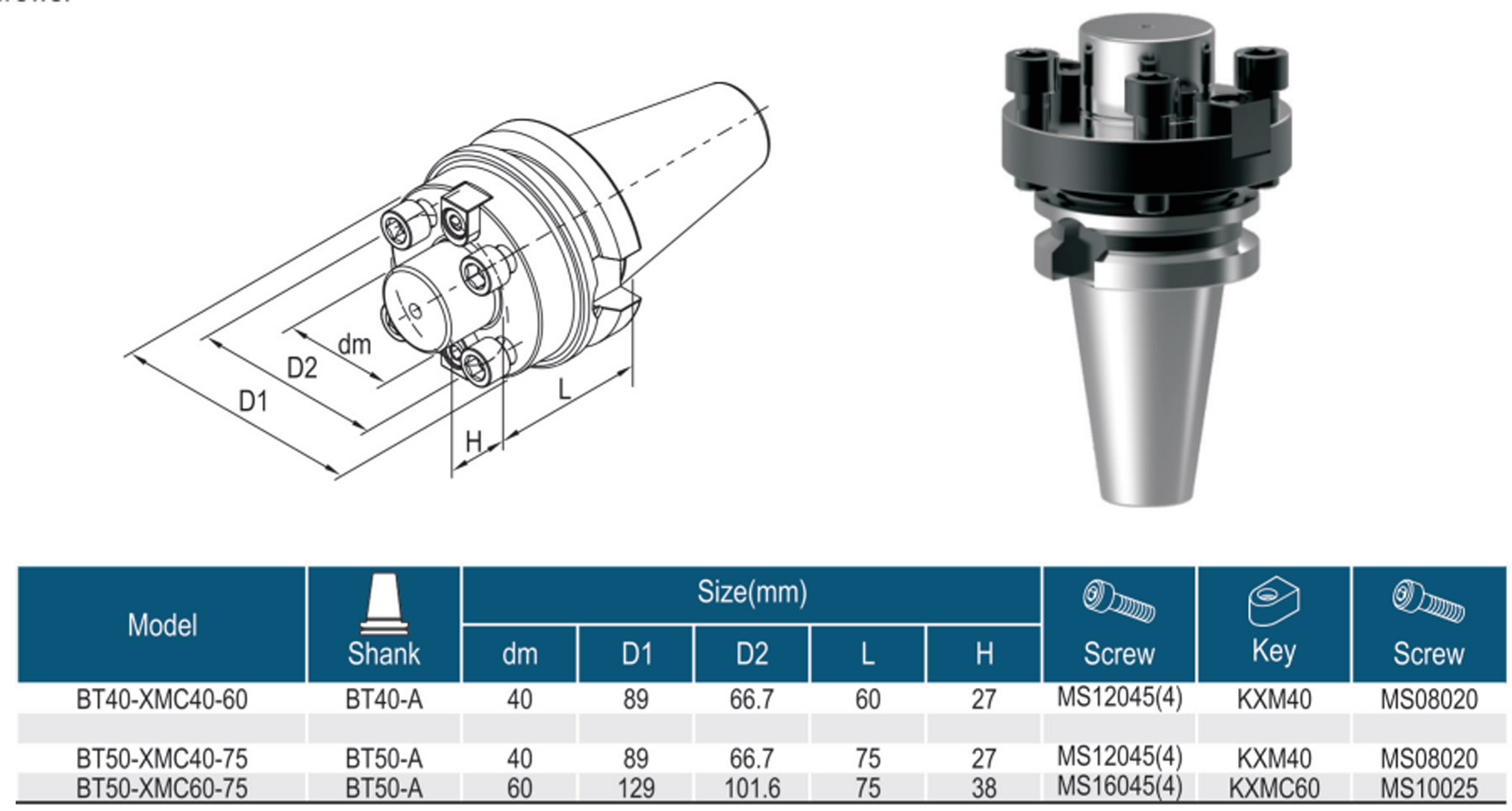
Function
The primary function of the face milling cutter holder is to securely clamp the face milling cutter to the machine spindle with high precision, enabling efficient and accurate cutting operations. Face milling cutters are mainly used for machining the surface of workpieces, with a wide range of applications in rough and finish machining of materials such as steel, cast iron, and aluminum alloys. The stability of the holder directly affects the smoothness and quality of the milling process. The increased collar contact surface provides greater support, reduces tool vibration, improves cutting precision, and extends the tool’s service life.
Usage Instructions
Tool Setup: Align the four mounting holes of the face milling cutter with the lock screw holes on the holder, ensuring the cutter is properly positioned. Use the supplied lock screws to fasten the cutter, tightening them to the appropriate torque to prevent loosening during operation.
Holder Installation: Depending on the required shank size (BT40 or BT50), insert the holder into the CNC machine’s spindle. Ensure the spindle and holder are tightly connected, and use a pull stud to secure the holder firmly.
Machining Operations: Start the machine and perform a test cut to check the stability of the tool and the surface quality of the workpiece. If the cutting is smooth and the surface finish meets the requirements, proceed with full-scale machining.
Usage Precautions
Use of Lock Screws: Ensure the lock screws are evenly tightened when installing the face milling cutter to prevent misalignment, which can lead to instability during operation. Pay attention to the tightening torque to avoid over- or under-tightening, which can affect tool performance.
Clean Collar Contact Surface: The collar contact surface is the primary support between the holder and the tool. Before use, make sure this area is clean and free from debris. Any foreign material can compromise the clamping force, leading to vibration or slippage during cutting.
Fit Between Holder and Spindle: When installing the holder into the machine spindle, ensure the mating surfaces are clean and smooth. Regularly inspect the holder’s taper to ensure it is undamaged or unworn. If the taper is damaged, replace or repair it promptly to maintain machining accuracy.
Operating Environment: Avoid using the holder in extreme environments, such as high-temperature or humid conditions, which may cause material deformation or rusting, impacting its service life and machining precision.
Regular Maintenance: The holder is a precision tool that requires regular cleaning and inspection after use, especially checking the condition of the lock screws. If any screws show signs of wear or aging, they should be replaced promptly.
Contact: Jason Lee
Email: jason@wayleading.com
Post time: Sep-30-2024