A Morse taper holder (Morse Taper Holder) is a commonly used machine tool accessory, widely applied in the field of machining, especially on drills, lathes, milling machines, and other equipment for holding tools or accessories with a Morse taper (MT, Morse Taper). This article mainly introduces a Morse taper holder with a JT model shank, its functions, usage, and precautions.
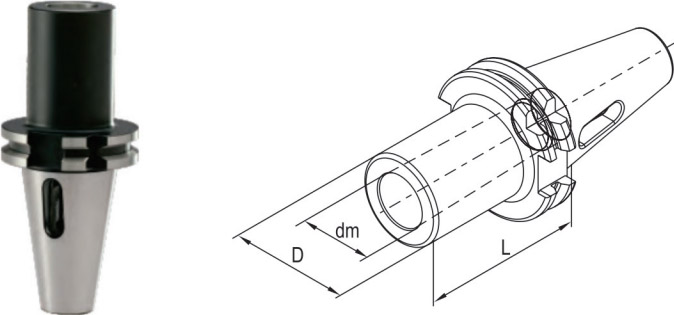
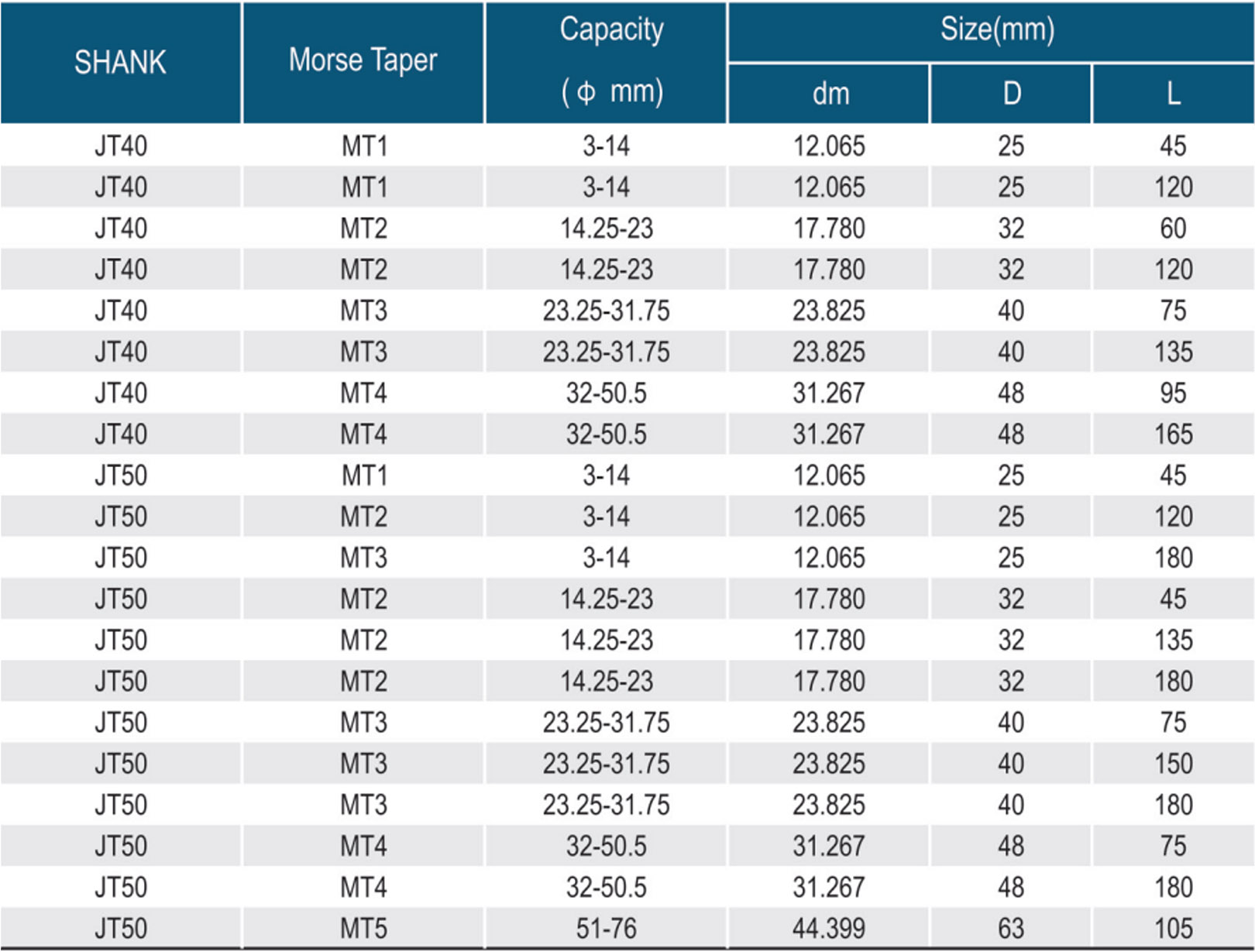
Functions
The primary function of a Morse taper holder with a JT shank is to provide secure tool clamping and precise positioning. The Morse taper design generates a strong clamping force through the taper fit, ensuring that the tool remains stable and does not slip during machining. The JT (Jacobs Taper) shank is typically used to fit the Morse taper holder into the machine spindle or another fixture. Therefore, this holder combines two tapers: one end features a JT taper for fitting into the machine spindle, while the other end accommodates tools or accessories with an MT taper,like the taper shank twist drill. Common Morse tapers range from MT1 to MT5, suitable for different diameters and tool specifications.
Usage
Tool installation: First, insert a tool with a Morse taper (such as a taper shank twist drill., reamer, or taper sleeve) into the MT hole of the Morse taper holder. The friction from the taper fit naturally secures the tool, but to ensure firm clamping, a light tap on the tool's end with a mallet may be necessary to ensure it is fully seated.
Holder installation: Insert the JT taper end into the machine spindle or another holding device. The JT taper is self-locking, meaning once clamped, it will hold tightly and is difficult to loosen, ensuring the tool will not move or shift during machining.
Machining operation: After the tool is securely mounted, drilling, reaming, or turning operations can be carried out. Due to the self-locking nature of the Morse taper, the tool remains stable even under high cutting forces.
Precautions
Cleaning and maintenance: Before each use, ensure that the tapered surfaces of both the holder and the tool are clean, free of oil or debris. Dirt or foreign matter can affect the accuracy of the taper fit, potentially causing the tool to loosen, which may impact machining precision or lead to accidents.
Avoid excessive hammering: Although the taper connection has good self-locking properties, excessive hammering may cause deformation or wear of the taper, which can reduce the clamping force and lifespan. When installing the tool, tap lightly to ensure it is properly seated without excessive force.
Regularly check for taper wear: Wear on the taper can cause the tool to be inadequately secured. It is recommended to periodically inspect the taper fit to ensure the surface is smooth and free of scratches. If significant wear is found, the holder should be replaced or repaired to avoid performance issues.
Use the correct tool specifications: Different Morse taper sizes correspond to different tool diameters. When using the holder, ensure that the taper sizes of the holder and tool match to prevent unstable clamping or tool dropout due to a mismatched fit.
Safe operation: When using tapered tools, always follow machine operating procedures. Avoid suddenly loosening the tool during high-speed or heavy-load operations to ensure the operator's safety.
Contact: Jason
Email: jason@wayleading.com
Post time: Oct-13-2024