The Milling Chuck is a high-precision clamping tool specifically designed for machining operations, typically used to secure tools with a BT shank. It provides strong clamping force and high stability, significantly enhancing surface quality and extending tool life. Through an optimized design, the chuck achieves ideal damping characteristics and low vibration, making it suitable for high-speed machining applications. With radial runout kept below 0.01mm, it ensures machining precision. The Milling Chuck is commonly used in milling operations and is ideal for applications with stringent quality requirements, such as mold manufacturing and precision parts machining.
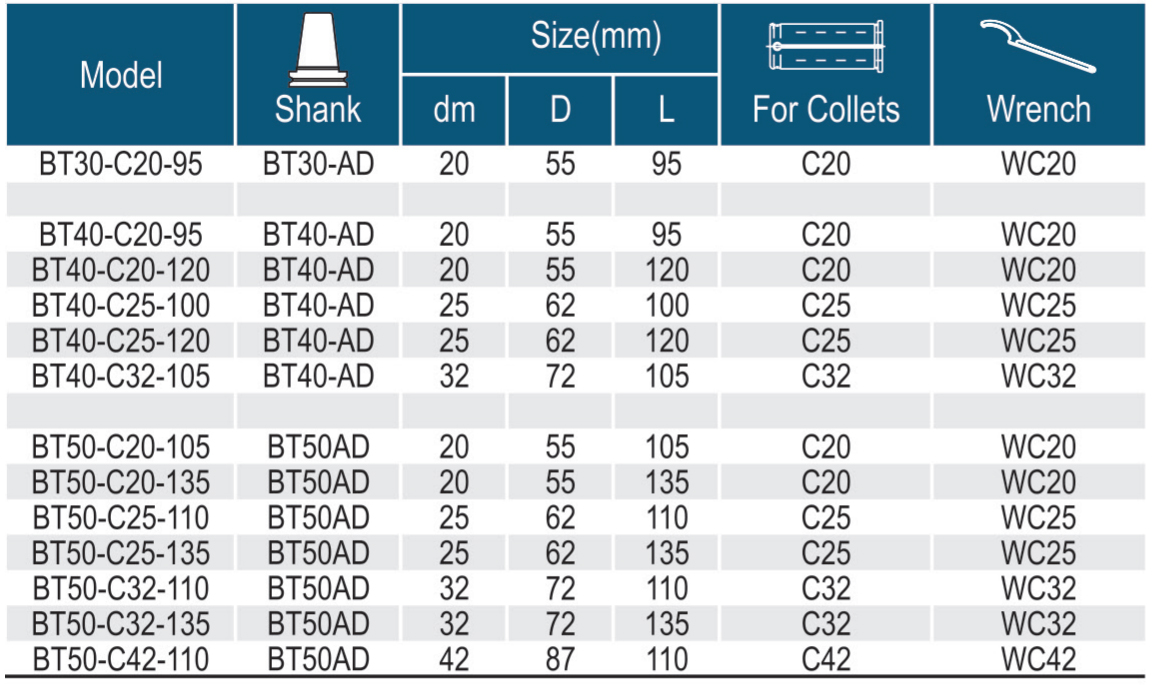
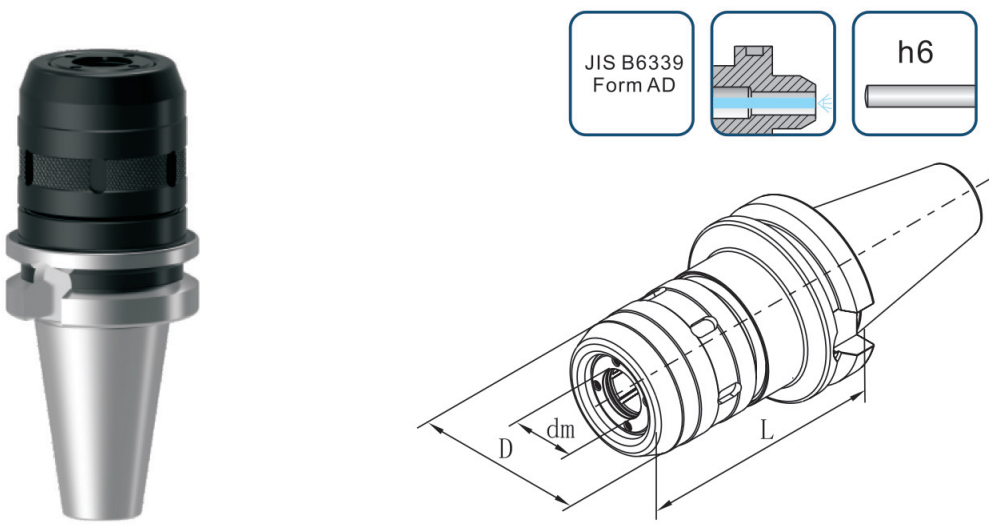
Usage Instructions
Installing the BT Shank Tool: Insert the tool’s BT shank into the chuck, ensuring that the tool is fully seated. The BT shank is a standard taper, suitable for high-speed and high-precision machining environments.
Clamping: Use a specialized wrench or tool to tighten according to the specified torque in the manual. The Milling Chuck is designed to provide strong clamping force, but be careful not to exceed the recommended torque to avoid damaging the chuck or tool.
Adjusting Clamping Range: The Milling Chuck supports the use of reduction sleeves, allowing it to fit tools of different diameters. Select the appropriate sleeve based on the tool’s dimensions to ensure a secure grip.
Checking Clamping Condition: Before starting the machine, carefully check the tool’s clamping condition to ensure it is fully secure, preventing looseness during machining that could affect precision or cause safety issues.
Usage Precautions
Avoid Over-tightening: Although the Milling Chuck provides high clamping force, avoid over-tightening to prevent damage to both the tool and chuck. Excessive force on BT shank tools can impact machining accuracy.
Regular Radial Runout Calibration: The Milling Chuck guarantees radial runout below 0.01mm, which is critical for high-precision machining. Regularly check the radial runout of the chuck to ensure compliance with this requirement.
Maintain Cleanliness: Clean the chuck and tool surfaces before use to remove any oil or particles, which will ensure optimal clamping force and machining precision. Regular maintenance of the chuck’s cleanliness can also extend its lifespan.
Tool Replacement Safety: Ensure the machine spindle and equipment are completely shut down before replacing the tool to avoid accidental operation and potential hazards.
Verify Reduction Sleeve Suitability: For tools of different shank diameters, choose the correct reduction sleeve. An incorrect sleeve could lead to insufficient clamping or runout during machining, affecting quality.
Contact: Jason Lee
Email: jason@wayleading.com
Post time: Oct-27-2024