Precision Dial Indicator Gage For Industrial With Jeweled
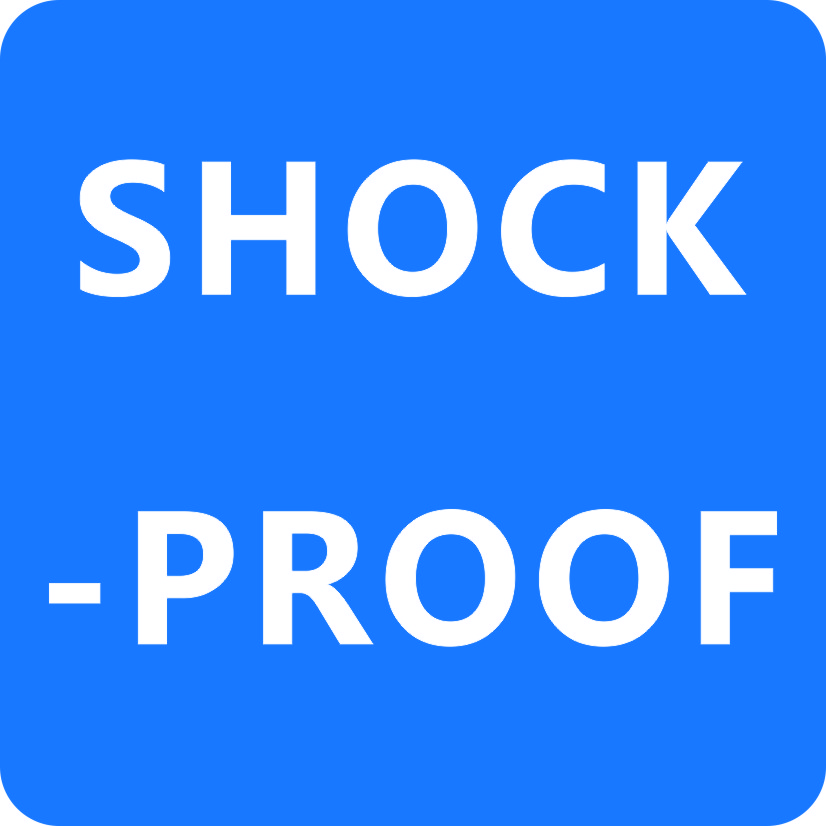
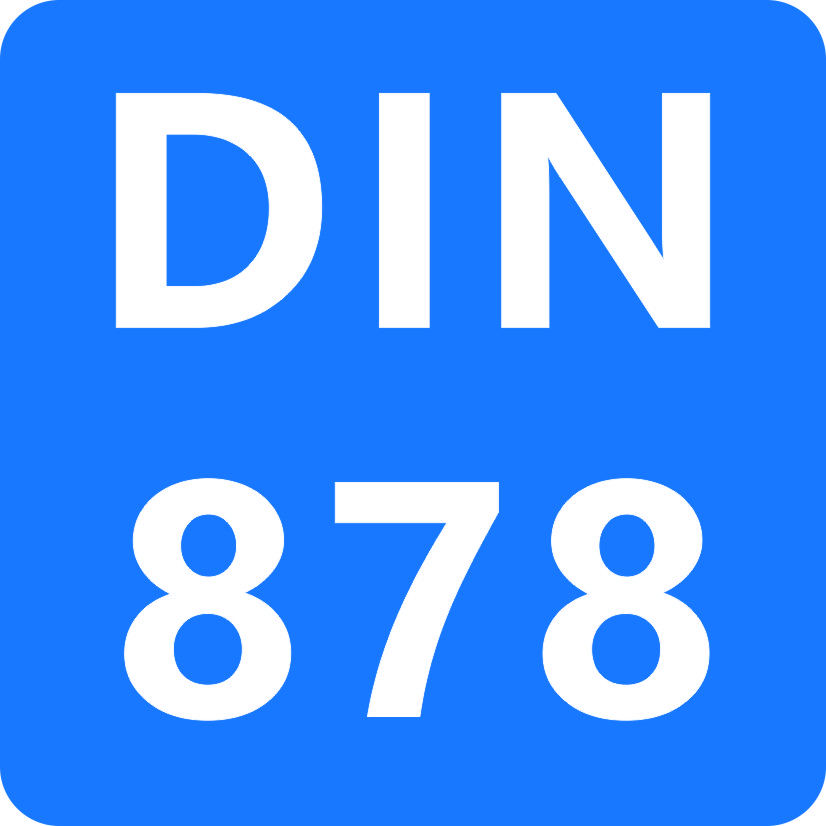
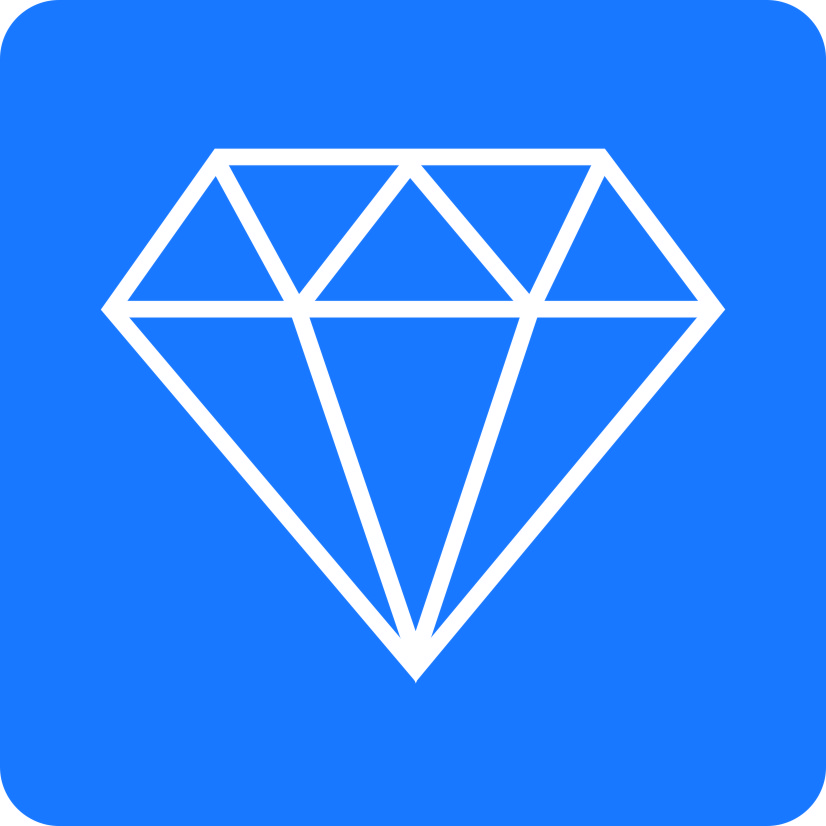
Dial Indicator Gage
● Used to measure surface flatness as well as axial runout and also used to check tool set up and squareness.
● Limit indicator clips inclued.
● Strictly made in accordance with DIN878.
● Jeweled bearings providing the lowest possible bearing friction.
● With narrowed range and higher accuracy.

Range | Graduation | Dia. Size | Order No. |
0-3mm | 0.01mm | 42mm | 860-0873 |
0-8mm | 0.01mm | 42mm | 860-0874 |
0-5mm | 0.01mm | 58.5mm | 860-0875 |
0-10mm | 0.01mm | 58.5mm | 860-0876 |
0-20mm | 0.01mm | 58.5mm | 860-0877 |
0-25mm | 0.01mm | 58.5mm | 860-0878 |
0-30mm | 0.01mm | 58.5mm | 860-0879 |
0-50mm | 0.01mm | 80mm | 860-0880 |
0-1" | 0.01mm | 58.5mm | 860-0881 |
Precision in Machine Tools: Dial Indicator Application
The dial indicator, a stalwart in the field of precision engineering, finds extensive application in machine tools, contributing to accurate measurements and quality control. This tool, with its finely calibrated dial and robust design, plays a crucial role in various industries, ensuring precision in machining processes.
Machine Tool Calibration and Setup
One primary application of the dial indicator is in calibrating and setting up machine tools. Machinists use this tool to measure runout, alignment, and perpendicularity, ensuring that machines are precisely configured. By verifying the accuracy of tools and equipment, the dial indicator aids in achieving optimal performance in machining operations.
Surface Flatness and Straightness Measurements
In the machining of critical components, such as engine parts or aerospace elements, maintaining surface flatness and straightness is imperative. The dial indicator excels in measuring deviations from flatness or straightness, providing machinists with real-time feedback. This application ensures that the finished products meet stringent quality standards.
Checking Part Tolerances and Dimensions
The dial indicator is a go-to tool for inspecting part tolerances and dimensions during and after the machining process. Whether measuring the depth of a bore or ensuring the correct diameter of a hole, the dial indicator’s precision and ease of use make it indispensable for machinists striving for accuracy in their work.
Runout and Eccentricity Verification
When components rotate, runout and eccentricity can impact performance. The dial indicator aids in measuring these parameters, allowing machinists to identify and correct any deviations. This application is particularly crucial in industries such as automotive manufacturing, where components like brake rotors require precise runout for optimal functionality.
Quality Control in Manufacturing
In the broader scope of manufacturing, the dial indicator is a key tool for quality control. Its versatility allows machinists to perform various measurements, contributing to the overall quality assurance of machined parts. This ensures that the final products meet design specifications and comply with industry standards.
Efficient and Reliable Measurement
The dial indicator’s simplicity, coupled with its high precision, makes it an efficient and reliable tool in machine tool applications. Its easy-to-read dial and sturdy construction withstand the rigors of industrial environments. From fine-tuning machine setups to verifying part dimensions, the dial indicator remains a cornerstone in the pursuit of accuracy in machining processes.
Advantage Of Wayleading
• Efficient and Reliable Service;
• Good Quality;
• Competitive Pricing;
• OEM, ODM, OBM;
• Extensive Variety
• Fast & Reliable Delivery
Package Content
1 x dial Indicator
1 x Protective Case
1 x Inspection Certificate
Please contact us for further information. To assist you more effectively, Kindly provide the following details:
● Specific product models and the approximate quantities you require.
● Do you require OEM, OBM, ODM or neutral packing for your products?
● Your company name and contact information for prompt and accurate feedback.
Additional, we invite you to request samples for quality testing.